イートン、車両部品やコンポーネント製造に3D金属プリントを開始
リードタイム短縮や効率性向上、コスト削減
イートンは、インダストリー4.0戦略の一環として、車両グループが、開発時間を短縮し効率を向上させるための新しい3D金属プリントプログラムを実装することを発表した。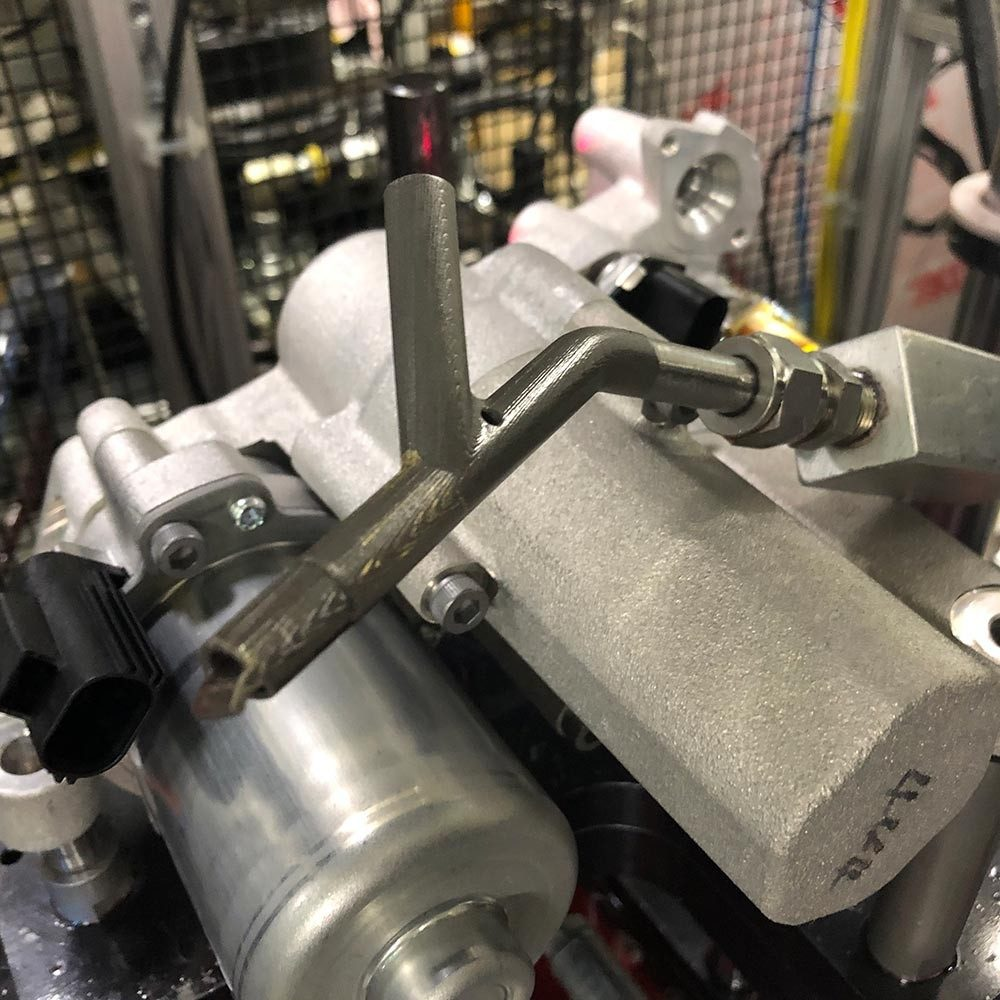
3Dプリンターは、高品質の器具、安全装置、組み立てと管理のためのオートメーショングリッパー、さらに、交換が必要なメンテナンスコンポーネントを製造するために利用される。
プロトタイプ開発はより迅速な製品開発試験をサポートし、効率性を向上させるための戦略に従っている。
設計プロセスをスピードアップするために、スキャナーを使用して、既存のコンポーネントの3Dモデルを作成する。このプロセスにより、コンポーネントはリバースエンジニアリングされ、使用する材料を削減するように設計を変えること、様々な位置要素の追加、複数コンポーネントを単一部品に統合するなど、3Dプリント機能をより有効に活用できる。
3Dプリンターが世界展開され数が増えるにつれて、イートンの自動車グループは、リードタイム短縮やコスト削減など、さらなる運用の改善を実現していく。
3Dプリント技術では、必要な場所にのみ材料を追加し、より高度なデザインを開発でき、これらの2つの要素が合わさり、材料費を削減しながら、必要な後処理作業の量も削減する。
必要に応じて、熱処理や化学浴なども追加
金属部品およびコンポーネントをプリントするプロセスは、ロッドに保管され、ワックスとポリマーバインダーによって一緒に保持されている粉末金属を使用して始められる。押し出されると同時に溶けた金属を使用し、3Dプリンターは、プログラムされた回路図に基づいて、レイヤーを次々と追加していく。プリントプロセスが完了すると、部品またはコンポーネントを化学浴に通して、ポリマーバインダーの大部分を除去する。次に、部品を炉に通過させて残りのワックスとポリマーを除去し、金属材料を高密度構造に融合させる。
プリントされた部品やコンポーネントの用途や、使用された材料に応じて、追加の熱処理プロセスが、部品の強度をさらに高めるために実行される。
コンポーネントをプリントするための合計の所要時間は、パーツのサイズや複雑さなど、いくつかの基準によって異なる。部品やコンポーネントの設計や必要な許容差によっては、後処理を行うこともできる。
デバインダー操作と熱処理はバッチで行われ、次のコンポーネントがプリントをする間、いくつかの異なるコンポーネントがこれらのプロセスを一緒に通過する。
プリンター、デバインダー操作、炉作業は統合されたループで動作するが、デバインダー操作または炉作業を追加実行することなくプリント数を増やすという柔軟性も提供している。
イートンは、今後、車両グループの3Dプリント機能により、生産時間をさらに短縮し、効率性を向上させる。
(画像はプレスリリースより)
▼外部リンク
Eaton Press Releases
https://www.eaton.com/